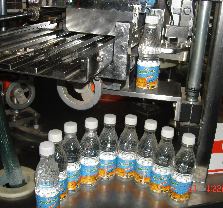
The Design Process of a Filling Machine
Designing a filling machine is an intricate dance of engineering and functionality. It begins with understanding the product being filled—be it liquids, powders, or granules. Each type requires specific considerations.
Next comes the selection of technology. Will gravity work best for your application, or does vacuum sealing make more sense? The choice can vastly affect efficiency and accuracy.
Prototyping plays a crucial role in this phase. With computer-aided design (CAD) software, engineers create detailed models to visualize how components interact. This step ensures that potential issues are identified early on.
User experience is also essential; controls must be intuitive to minimize operator error. This aspect contributes significantly to overall productivity.
Safety features are integrated into the design to protect both products and personnel during operation. Achieving a harmonious blend of these elements defines successful filling machine design.
Materials Used in Filling Machines
Filling machines rely on a variety of materials to ensure durability and efficiency. Stainless steel is the gold standard for many components due to its resistance to corrosion and easy cleaning. This material is essential, especially in industries dealing with food and pharmaceuticals.
Plastic materials also play a crucial role. They are lightweight, cost-effective, and resistant to certain chemicals. High-density polyethylene (HDPE) is often used for parts that require flexibility without compromising strength.
Rubber seals are vital too. They prevent leaks during the filling process while offering flexibility under pressure. The choice of rubber compounds can significantly affect performance; hence they must be selected carefully based on the liquid being filled.
In more advanced systems, specialized alloys may be utilized for enhanced strength or thermal management—important factors in maintaining product integrity during filling operations. Each material contributes uniquely to the functionality of these machines, underscoring their complexity.
The Different Types of Filling Machines
Filling machines come in various types, each designed for specific applications. Gravity fillers are among the simplest. They rely on gravity to dispense liquids into containers, making them ideal for thin fluids.
Piston fillers provide more precision. They use a piston mechanism to ensure accurate volume control, perfect for thick and viscous products like sauces or creams.
For powders and granules, auger fillers shine. These machines utilize a rotating screw to move product into the container efficiently.
Vacuum filling machines work wonders with highly foamy liquids by creating a vacuum that draws liquid into the bottle without overflow risks.
Then there are aseptic filling machines which maintain sterility throughout the process. This type is crucial in industries such as pharmaceuticals and food production where contamination must be avoided at all costs.
Each type plays its role in ensuring efficient and effective packaging solutions tailored to diverse industry needs.
The Filling Process: Step-by-Step Guide
The filling process begins with preparation. First, ensure that the machine is clean and calibrated for accuracy. This step is crucial to avoid contamination.
Next, containers are positioned on the conveyor system. Each container must be stable to prevent spills during filling. Operators monitor this setup closely.
Once everything is in place, the filling mechanism activates. Whether it’s gravity-fed or piston-driven, each method has advantages depending on the product type.
As the liquid fills each container, sensors detect when it reaches a predetermined level. This ensures consistency across all units produced in a batch.
After filling, containers often go through a capping or sealing stage. Proper sealing preserves freshness and prevents leaks during transport.
Filled products move to labeling stations where they receive important information before heading out for distribution. Each step plays an essential role in maintaining quality control throughout the entire process.
Quality Control in the Filling Process
Quality control plays a crucial role in the filling process. It ensures that every product meets specific standards before reaching consumers.
During this phase, various checks are conducted. These include evaluating fill levels, examining seal integrity, and verifying labeling accuracy. Each aspect is vital for maintaining brand reputation and consumer safety.
Advanced technology aids in quality assurance. Automated systems can detect inconsistencies such as underfilled or overfilled containers quickly. This allows for real-time adjustments to maintain optimal performance throughout production runs.
Additionally, regular audits of machinery are essential. They help identify potential issues before they escalate into larger problems that could affect output quality.
Trained personnel also contribute significantly to the quality control process by implementing standardized procedures and conducting routine inspections. Their expertise helps foster an environment where high-quality products become the norm rather than the exception.
Factors to Consider When Choosing a Filling Machine
Choosing the right filling machine requires careful consideration of several factors. First, assess your production volume. High-output operations may need a robust machine designed for speed and efficiency.
Next, consider the type of product you’re filling. Liquids, powders, or granules each demand different mechanisms and technologies to ensure precise dispensing without waste.
Compatibility with existing equipment is crucial as well. Seamless integration into your current setup can save time and reduce costs during installation.
Don’t overlook ease of operation and maintenance either. A user-friendly interface can minimize training times while regular upkeep ensures longevity.
Think about budget constraints. While it’s tempting to opt for the cheapest option available, investing in quality often leads to better performance and reliability in the long run.
Latest Innovations in Filling Machine Technology
The world of filling machines is rapidly evolving, driven by technological advancements. Recent innovations focus on automation and efficiency, making processes smoother than ever.
Smart filling machines equipped with IoT capabilities are gaining traction. These devices allow for real-time monitoring and data collection, enabling manufacturers to optimize operations effectively.
Another exciting development is the use of artificial intelligence in quality control. AI systems can detect inconsistencies in fill levels or packaging errors faster than human operators. This significantly reduces waste and enhances overall product quality.
Sustainability also plays a crucial role in modern designs. Many companies are now integrating eco-friendly materials into their machines while optimizing energy consumption during operation.
As industries continue to evolve, so will the technology behind filling machines—ensuring that they meet diverse demands efficiently and sustainably.
Conclusion
Understanding the filling machine process is crucial for anyone involved in manufacturing and packaging. Each step, from design to delivery, plays a significant role in ensuring efficiency and quality.
By grasping the intricacies of how these machines are designed and built, you can appreciate the thoughtfulness that goes into material selection and functionality. Different types of filling machines cater to various products—be it liquids, powders, or granules—and knowing which one suits your needs makes all the difference.
The filling process itself requires precision at every stage. Quality control checks ensure that each product meets industry standards while maintaining consistency across batches. Selecting the right machine involves careful consideration of several factors tailored to your specific production requirements.
Regular maintenance ensures longevity and optimal performance, safeguarding your investment over time. As technology continues to evolve, keeping up with innovations can provide competitive advantages in an ever-changing market landscape.
Understanding this entire process empowers manufacturers to streamline operations while delivering high-quality products efficiently.