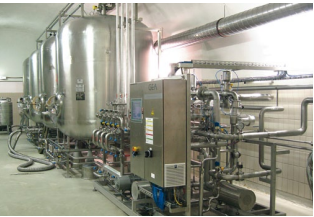
Introduction to Filling Machines
Filling machines are the unsung heroes of the food and beverage industry. They work tirelessly behind the scenes, ensuring that products meet both consumer expectations and regulatory standards. As businesses grow, maintaining quality becomes increasingly challenging. This is where filling machines step in, transforming production lines and elevating quality control to new heights.
Imagine walking into a grocery store and seeing rows of perfectly packed beverages or neatly filled jars of sauces. Each product represents hours of meticulous planning, precise measurements, and stringent checks—all made possible by efficient filling machinery. The impact these machines have on quality control cannot be overstated; they play a pivotal role in safeguarding not just brand reputation but also consumer safety.
Let’s dive deeper into how filling machines are revolutionizing quality assurance in this vibrant sector, making every drop count while keeping standards sky-high.
Importance of Quality Control in the Food and Beverage Industry
Quality control is a cornerstone of the food and beverage industry. It ensures that products are safe for consumption and meet regulatory standards. This process not only protects consumers but also builds brand trust.
In an age where health concerns are paramount, quality control helps companies maintain high safety standards. Regular inspections and testing can prevent contamination or spoilage, which could otherwise lead to serious consequences.
Moreover, consistent quality enhances customer satisfaction. When people know they can rely on a specific brand for delicious taste and freshness, they become loyal advocates.
Additionally, effective quality control minimizes waste and reduces costs associated with defective products. This balance contributes to overall efficiency in production processes while supporting sustainability efforts within the industry.
How Filling Machines Improve Quality Control Processes
Filling machines play a crucial role in enhancing quality control within the food and beverage sector. By automating the filling process, they minimize human error, ensuring that each container receives an accurate volume.
These machines are equipped with advanced sensors that detect variations in fill levels. If any discrepancies occur, production halts until adjustments are made. This immediate feedback loop fosters consistency across batches.
Moreover, many modern filling machines offer real-time monitoring capabilities. Operators can track performance metrics like speed and accuracy at a glance. Such transparency leads to proactive maintenance and quicker problem resolution.
Additionally, integrating these machines with software solutions allows for comprehensive data analysis. Businesses can identify trends over time, enabling them to adapt processes based on solid evidence rather than guesswork.
The precision provided by filling machines reinforces trust among consumers while preserving product integrity from factory to shelf.
Types of Filling Machines Used in the Food and Beverage Industry
The food and beverage industry employs various types of filling machines, each designed for specific applications. Piston fillers are popular for their accuracy, making them ideal for thicker products like sauces or purees.
Gravity fillers work well with lighter liquids such as juices and soft drinks. They rely on gravity to dispense the product into containers, ensuring a smooth flow without excessive pressure.
For carbonated beverages, vacuum fillers are often used. These machines minimize foaming by creating a vacuum that draws liquid into the container swiftly.
Another common type is the rotary filler. This machine offers high-speed filling capabilities and is commonly found in bottling plants. It maximizes efficiency while maintaining precision in volume control.
Aseptic filling systems play a crucial role in preserving product freshness. They ensure that both product and packaging remain sterile throughout the process, extending shelf life significantly.
Case Studies of Companies Using Filling Machines for Quality Control
A leading beverage company recently integrated advanced filling machines into their production line. They noticed a significant reduction in product variance, ensuring that every bottle met strict quality standards. With precise measurements and automated processes, they eliminated human error during filling.
Another example comes from a gourmet food manufacturer. By using vacuum filling machines, they maintained the integrity of delicate products like sauces and spreads. This method preserved flavor profiles while extending shelf life.
An organic juice producer adopted high-speed gravity fillers to enhance efficiency without compromising quality. Their commitment to natural ingredients remained intact as these machines minimized oxidation during processing.
These case studies illustrate how companies are leveraging technology for superior quality control in the food and beverage sector. Each story highlights unique challenges faced and the innovative solutions provided by modern filling machinery.
Potential Challenges and Solutions for Implementing Filling Machines in Quality Control
Implementing filling machines in quality control isn’t without its hurdles. One major challenge is the initial cost of acquisition and installation. Many companies may hesitate to invest heavily upfront.
Training staff can also be a significant obstacle. Employees need proper training to operate these sophisticated machines effectively. Without this, even advanced technology may not yield optimal results.
Moreover, integrating new machinery with existing processes could pose complications. Compatibility issues might arise, leading to production delays or inefficiencies.
To tackle these challenges, businesses should consider phased implementation strategies. This approach allows for gradual adaptation while minimizing disruptions.
Investing in comprehensive training programs ensures that staff are confident and efficient when using new equipment. Regular maintenance schedules can also mitigate potential breakdowns, ensuring consistent performance over time.
Future Developments and Advancements in Filling Machine Technology
The future of filling machine technology is on the brink of transformation. Innovations are emerging that promise to enhance accuracy and efficiency like never before.
Smart technologies, such as IoT integration, are paving the way for real-time monitoring. This allows operators to track performance metrics and quickly address any anomalies during production.
Another exciting development is the rise of automated cleaning systems. These make maintenance easier while ensuring hygiene standards are met consistently without extensive downtime.
Moreover, advancements in artificial intelligence will enable machines to adapt their processes based on changing product characteristics or packaging requirements. This level of flexibility can significantly boost productivity across various sectors within food and beverage manufacturing.
Sustainability also plays a critical role in future designs. More manufacturers are focusing on eco-friendly materials and energy-efficient operations, contributing positively to both business practices and environmental impact.
Conclusion: The Role of Filling Machines in
The role of filling machines in the food and beverage industry is crucial. These machines are not just about efficiency; they directly influence product quality and safety. As companies strive to meet stringent regulations, the accuracy provided by modern filling technology becomes indispensable.
Filling machines enhance consistency across batches, minimizing human error that can lead to variations in product quality. This helps maintain brand reputation, ensures customer satisfaction, and fosters trust among consumers.
Moreover, with advancements in technology such as smart sensors and automation, these machines will continue to evolve. Future developments promise even greater precision and integration within wider production systems.
Investing in high-quality filling machinery stands out as a significant step toward optimizing production processes while prioritizing quality control. The impact of these innovations resonates throughout the entire supply chain, ultimately benefiting both producers and consumers alike.