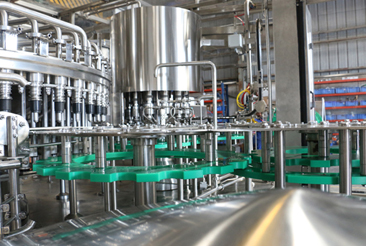
Introduction to Can Fillers
Can fillers are the unsung heroes in the world of beverage production. Imagine a bustling brewery or a small craft soda shop where every can is filled with precision and care, ensuring that each sip delivers an explosion of flavor. In today’s market, efficiency and quality are paramount, especially when it comes to carbonated beverages. Can fillers play a crucial role in achieving this balance.
These machines have evolved over the years, adapting to meet the demands of both large-scale manufacturers and artisanal creators alike. Whether you’re producing fizzy drinks or exploring other liquid innovations, understanding can fillers is essential for anyone in the industry. Let’s dive into what makes these machines so vital and discover how they stand out as perfect solutions for carbonated beverages and more.
Types of Can Fillers Available
Can fillers come in various types, each designed for specific needs and production scales. The most common are gravity fillers, which use the force of gravity to fill cans. They work best with low-viscosity liquids.
Pressure fillers are another option. These employ pressure to push the beverage into cans, making them ideal for carbonated drinks. This method helps maintain carbonation levels and ensures precise filling.
There are also volumetric fillers that measure liquid by volume before dispensing it into the can. This type is great for achieving consistent levels across all containers.
Rotary fillers offer high-speed filling solutions for larger operations. They allow multiple cans to be filled simultaneously, increasing efficiency while maintaining quality control throughout the process. Each type has unique benefits tailored to different requirements in beverage production.
Advantages of Using Can Fillers
Can fillers offer a range of benefits that elevate beverage production. They enhance efficiency, allowing manufacturers to fill large volumes in a fraction of the time compared to manual methods.
Precision is another key advantage. Can fillers ensure consistent fill levels and minimize waste, leading to better cost management. This reliability helps maintain product quality across batches.
Moreover, can fillers improve hygiene standards during the filling process. Many modern machines are designed with easy-to-clean components, reducing contamination risks and ensuring safety for consumers.
Flexibility in design allows these machines to adapt to various can sizes and types. Whether it’s craft beer or sparkling water, producers benefit from versatility.
Automation reduces labor costs significantly. Fewer hands on deck mean lower operational expenses while still meeting production demands efficiently. The combination of speed and precision makes can fillers an essential tool for beverage creators today.
Applications of Can Fillers in Carbonated Beverages
Can fillers play a crucial role in the production of carbonated beverages. They ensure precise filling under pressure, preserving carbonation levels and maintaining taste integrity.
These machines are designed for high efficiency. They operate at impressive speeds while minimizing foaming during the filling process. This helps retain the beverage’s quality and ensures that every can is filled to perfection.
Moreover, can fillers accommodate various sizes and shapes of cans. Whether it’s sleek 12-ounce designs or larger formats, versatility is key in meeting market demands.
The technology involved allows for easy integration with other equipment like pasteurizers and labeling systems. This seamless connection enhances overall productivity on the production line.
Many manufacturers use can fillers not just for soft drinks but also craft beers and hard seltzers. As consumer preferences evolve, so does the need for reliable filling solutions that deliver quality consistently across all products.
Other Uses for Can Fillers
Can fillers aren’t just for carbonated beverages. They offer versatility across various industries.
Craft breweries often use them to package specialty beers, ensuring freshness and flavor retention. This is essential when targeting discerning customers who appreciate quality.
Juice producers also benefit from can fillers. These machines efficiently fill cans with fresh juice, preserving taste and nutrients while extending shelf life.
The food industry sees can fillers in action too—think soups or sauces. They provide a convenient packaging solution that appeals to busy consumers looking for quick meal options.
Even non-food products are embracing this technology. Household cleaners and personal care items find their way into cans, enhancing user experience through improved portability and durability.
This adaptability highlights the innovative spirit behind can filling technology, making it an invaluable asset across diverse markets.
Factors to Consider When Choosing a Can Filler
When choosing a can filler, think about the production capacity. The right size will depend on your output needs. A high-capacity model is great for large operations, while smaller systems suit niche markets.
Next, consider the type of beverage you’re filling. Different liquids require different equipment features. For carbonated drinks, look for fillers designed to handle pressure and maintain carbonation levels effectively.
Ease of use matters too. Look for intuitive controls and quick-change capabilities to minimize downtime during product swaps or maintenance.
Don’t forget about cleaning and sanitization requirements. Equipment that’s easy to disassemble simplifies hygiene processes and ensures compliance with health regulations.
Evaluate the cost versus longevity factor. Investing in quality may have a higher upfront cost but offers better durability and efficiency over time.
Maintenance and Upkeep of Can Fillers
Regular maintenance of can fillers is crucial for optimal performance. This ensures that machines run smoothly and efficiently, reducing downtime.
Start by establishing a routine cleaning schedule. Remove any residual product to prevent contamination or blockages. Pay close attention to the fill heads and valves as these areas are prone to buildup.
Lubrication is another key aspect. Check all moving parts regularly, applying appropriate lubricants where necessary. This reduces friction and extends the lifespan of your equipment.
It’s also wise to inspect components frequently for wear and tear. Identifying issues early can save you from costly repairs later on.
Don’t overlook software updates if your filler uses automation technology. Keeping systems updated enhances functionality and accuracy in filling processes.
Training staff on proper operation techniques further boosts efficiency while minimizing errors during production runs.
Conclusion
Can fillers are versatile and essential tools in the beverage industry, especially for carbonated drinks. They streamline the packaging process, ensuring efficiency while maintaining product quality. With various types available, businesses can choose a filler that best suits their production needs.
The advantages of using can fillers extend beyond just speed; they enhance consistency and reduce waste. This makes them an attractive option for companies looking to scale their operations without sacrificing standards.
While carbonated beverages remain the primary application for these machines, their functionality is not limited to this area. Can fillers also cater to juices, teas, and alcoholic beverages—showcasing their flexibility across different markets.
Choosing the right can filler requires careful consideration of factors such as production volume, type of beverage being packaged, and budget constraints. Regular maintenance is equally crucial to ensure optimal performance over time.
With innovation driving advancements in technology and design, can fillers continue to evolve. They stand out as perfect solutions for carbonated beverages—and much more—making them indispensable in today’s competitive landscape.