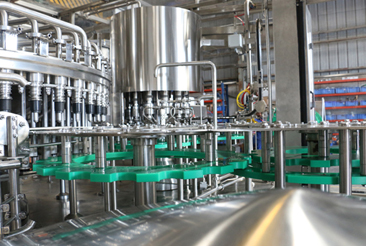
The purpose of slide bearings, also known as sliding or plain bearings, is to lessen friction between rotating, reciprocating, or sliding surfaces like shafts and stationary surfaces like housings.
Although they go by a variety of names, fluid-film bearings are a class of mechanical parts that fall under this heading. Although water may occasionally be utilized in specific circumstances, oil typically serves as the lubricating film.
“Dry running” bearings get their slipperiness through the use of PTFE or other low-friction compounds. Slide bearings use different rolling parts than ball and roller bearings do to reduce friction, although the end result is the same in both instances. Sliding bearings can be categorized in a purpose of ways, but for the sake of this article, their substance is explored.
1. Babbitt bearings and bronze
The shafts of many big rotating devices, including steam turbines, are supported by fluid-film bearings, also known as journal bearings. Practically all engines, including those in automobiles, perform the same function. Leaded bronze, copper lead, tin bronze, and other copper alloys, as well as conformable materials like tin- or lead-based babbitts, are frequently used to make these bearings.
2. Carbon insert bearings
In many instances where the environment is too abrasive for rolling-element bearings, graphite is employed as a shaft lubricant. In the standard design, cast bronze is machined to the bearing’s dimensions, and holes are drilled through the outer surface and into the bearing’s inner surface. The holes are subsequently filled with graphite plugs. Sintered bronze with steel backings and a graphite impregnation are some variations that allow for both dry and self-lubricated operation. High-temperature environments frequently employ graphite bearings.
3. Polymer bearings
The newest method to slide bearings is polymer bearings, which are typically coiled with lubricating strands or injection molded with solid lubricants. A thin metal shell is frequently joined with the high slip material PTFE to create a slide bearing that may operate without cold flow. These bearings’ effective range can be reduced by heat; to dissipate the heat generated during operation, metal shells are occasionally utilized. The lubricant is typically spread throughout the bearing body of molded polymer bearings. Any of these bearings may be impacted by humidity-related swelling. For usage in humid areas, many manufacturers offer bearings constructed with low moisture-absorbing materials.
4. Selection and sizing
Fluid-film bearings are governed primarily by three factors: viscosity, rotating speed, and bearing unit load. Three key presumptions must be true for hydrodynamic lubrication to work: that the shaft and bearing are moving in relation to one another; that the shaft is moving eccentrically up the bearing wall; and that the bearing contains an appropriate fluid.