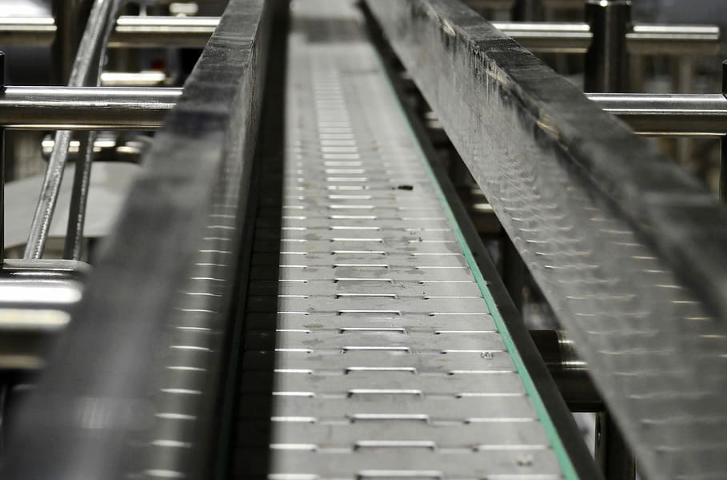
There is a variety of conveying technologies to choose from. The first step is to educate yourself on the various varieties and the ideal markets for which they are most effective. The pros and disadvantages of the various types of bulk material handling conveyors are listed below.
1. Conveyor Belt
The belt conveyor is the first conveyor we’ll look at. Belt conveyors’ primary advantages are distance and the ability to transport material from mines and pits to processing plants over long distances. Belt conveyors also have a high capacity rating, which is an additional benefit. This means they can handle a large volume of material at a faster rate.
However, because the belt conveyor only uses 20-25 percent of the actual space to carry material, it would have to be rather enormous to transport tons of material. Another downside of this form of conveyor for bulk material handling is that if you’re transporting dangerous, dusty, or explosive material, you’ll need external dust control equipment.
2. Screw Conveyor
The screw conveyor is the second conveyor option. The screw conveyor is a very typical form of bulk material handling conveyor. This is because it can handle a wide range of materials, has a simple working structure, and has a low initial investment compared to other conveying technologies. A screw conveyor has an advantage over a belt conveyor in that there is less external equipment required to prevent dusting and contamination.
The amount of horsepower required to drive this sort of screw conveyor is a drawback due to the torque needs, which can be large depending on the type of material and density. Another disadvantage of this sort of conveying system is the potential for material degradation. If you need to retain the nature of your product intact during material transfer, screw conveyors aren’t the best option. According to a study conducted by FML, the screw conveyor degraded material by 6%.
3. En-Masse Conveyor
Last but not least, there’s the En-Masse drag chain conveyor. The En-Masse drag conveyor is a material-moving system that is both efficient and cost-effective. It allows for a high-volume material flow in a limited space. The En-Masse drag conveyor uses 90% of its physical space for conveying, compared to the belt conveyor stated above. As a result, it will take up far less area than a screw conveyor to carry the same amount of material, if not more. The En-Masse drag conveyor also has the advantage of using less energy and having lower maintenance costs than its competitors, despite the fact that it can carry large amounts of material (thus the name). It also transports in a sealed container that protects it from contamination, dust, and hazardous materials.
Despite the fact that each conveyance method has its own set of benefits and drawbacks, some are clearly better suited for specific purposes. So, to figure out which is best for you, talk to a reputable conveyor manufacturer about what they recommend for your specific use.