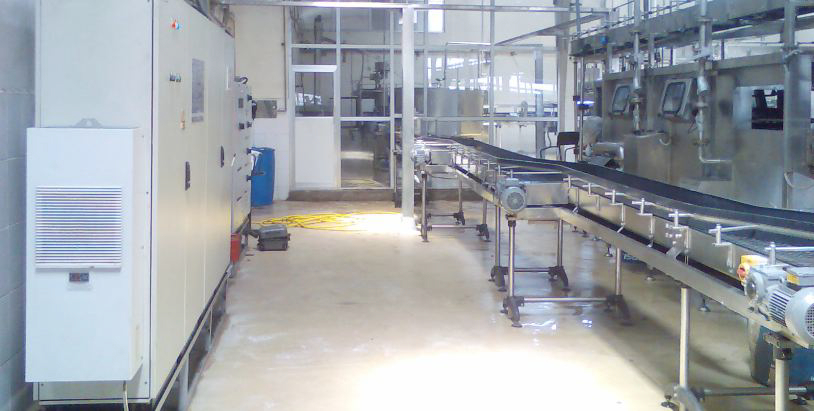
For handling dry bulk particles, a screw conveyor is one of the most versatile and cost-effective mechanical conveyors. The conveyor can carry materials from one or more inlet locations to one or more discharge points and offers enclosed transfer while moving materials horizontally, vertically, or at an incline. Because of the screw conveyor’s extensive choice of layouts, components, and construction materials, it can handle even the most difficult dry bulk materials.
A screw conveyor is made out of a screw that is positioned in a U-shaped trough (or tubular housing). The screw can be divided into one or more portions, each of which is made up of flighting fixed on a pipe. A revolving driving shaft is connected to one end of the screw, and an end shaft is connected to the other. At the trough ends, bearings support the screw. Hanger bearings dangling from the top of the trough can support the screw at locations between the screw sections if the screw conveyor is long enough to require further support.
1. Materials That Can Be Fluidized
When aerated or mechanically agitated, fluidizable materials – that is, materials that tend to flow like liquids – might flow uncontrollably through a screw conveyor. Alumina, Portland cement, powdered chocolate, fly ash, limestone dust, and talc are among the examples. Select a screw with a larger diameter and a short pitch to handle this type of material (that is, a short distance between flights). Flooding can be reduced by running the screw conveyor at a slower speed. If your material will discharge to a downstream weighing device, a double flight short pitch screw (which has two rows of flighting around the pipe) will help you better control the flow and decrease surging, resulting in a more uniform discharge to the weighing device.
2. Materials that do not flow freely
Viscous or sticky materials, materials that mat or interlock, and materials that pack are all materials of non-free-flowing materials. Green malt, sewage sludge, and wet beet sugar are examples of viscous or sticky materials. This material can collect in the screw flight-to-pipe joint and build upon the flight-to-pipe surfaces, decreasing conveying capacity. To handle a viscous or sticky material, use a single-flight ribbon screw with an open gap between the flight and pipe to prevent buildup on the screw, or a shaft less screw with a helical screw without a pipe in the center, which eliminates any potential for material to collect. Carbon black, hydrated lime, dried milk, talc, gypsum, and wood flour, which tend to pack under pressure, can produce many of the same difficulties as materials that tend to interlock.
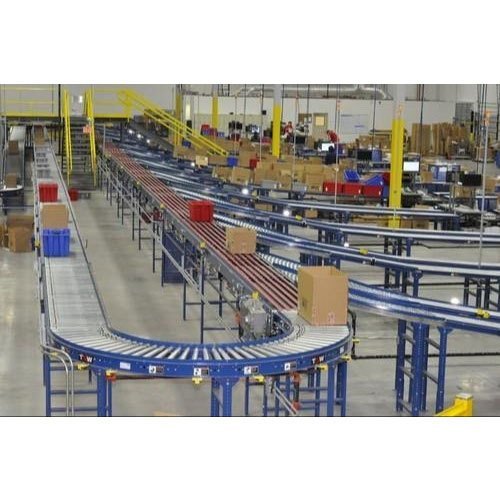
3. Materials Abrasive
Cement clinker, iron ore, foundry sand, whole soybeans, and titanium dioxide are all abrasive materials that can quickly wear out the screw conveyor’s components. If your material is abrasive, you can choose abrasion-resistant materials like hardened or hard-surfaced steel for the conveyor trough, screw, bearings, and other components. Abrasive wear can be reduced by conveying your material at a nominal depth of around 15% of the conveyor’s total capacity and running the conveyor at a modest speed.
4. hygroscopic Materials
Salicylic acid, dried milk powder, soap granules, and salt are hygroscopic materials that rapidly absorb moisture and can build up on screw flight surfaces and collect at the joint between the flight and the pipe. If your material is hygroscopic, choose a vapor- and material-tight screw conveyor with shaft seals and other seals to select wet air from coming into contact with it. To select material accumulation, either a single-flight ribbon screw or a shaftless screw. If your hygroscopic material is hot, such as a powder ejected from a dryer, you’ll want to maintain the screw conveyor heated to avoid the material coming into touch with cold air and causing condensation, which can moisten it.
5. Materials that are toxic or explosive
Toxic and explosive materials are dangerous and must be handled with care in a screw conveyor that is specifically designed to keep them contained. Toxic materials like asbestos, arsenic, benzene hexachloride, caustic soda, and lead oxide emit toxic fumes or dust that can escape the screw conveyor and endanger your workers’ health. Choose a screw conveyor with a vapor- and dust-tight housing if you’re dealing with the hazardous material. The shaft seals on the conveyor should be exceedingly tight, such as gas purged seals or flange type gland seals with several packing material rings. Use a dust management system at the conveyor discharge to capture and eliminate toxic gases and dust.
6. Collaborating with Your supplier
Expect to work closely with the engineering department of your screw conveyor supplier to verify that the conveyor you select will reliably handle your material. Conveyors for materials like yours have been designed by the supplier for years. During this procedure, you’ll need to supply thorough information about the qualities of your material, as well as your desired conveying rate, estimated conveyor usage, operating conditions, and other aspects. The supplier can handle screw conveyor testing using your material to show that the conveyor components and construction materials are capable of handling your difficult material and achieving your conveying objectives.