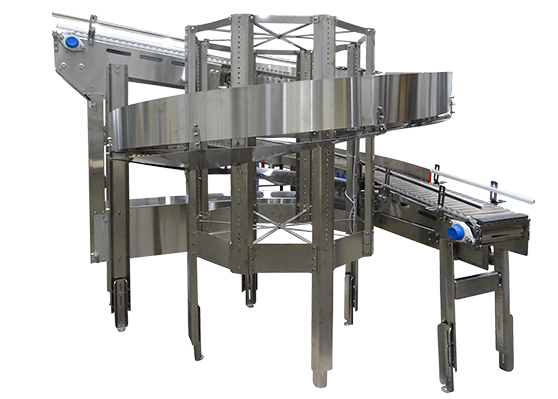
Introduction to Filler Machines
Filler machines are the unsung heroes of the packaging world. They streamline production, ensuring that everything from beverages to cosmetics is filled with precision and efficiency. But not all filler machines are created equal. With various types designed for different products, it can be overwhelming to navigate your options.
Whether you’re in the beverage industry or need a solution for personal care items, understanding the different types of filler machines available is crucial. This guide will walk you through each type—Pet, can, jar—and even explore some specialized options like tubes and pouches. By the end, you’ll have a clearer picture of which machine best suits your operations and needs. So let’s dive into this fascinating world of filling technology!
Types of Filler Machines
Filler machines come in various types, each tailored for specific packaging needs. Among the most common are pet filling machines, designed specifically for plastic containers like bottles. They ensure accuracy and efficiency when filling liquids or viscous products.
Can filling machines serve a different purpose. These robust units handle metal or aluminum cans, ideal for beverages and food products requiring hermetic sealing.
Jar filling machines focus on glass or plastic jars. They excel at accommodating thicker substances such as sauces or spreads while providing precise fill levels.
Beyond these three, other options exist, including tube fillers that dispense creams and ointments into collapsible tubes and pouch fillers suited for liquid or granular items packed in flexible pouches. Each type plays a crucial role in streamlining production processes across industries.
A. Pet Filling Machines
Pet filling machines are essential in the packaging industry, particularly for liquids like beverages and sauces. These machines are designed to handle the unique requirements of plastic containers, ensuring precise filling without spillage.
They come in various configurations, including gravity fillers and pressure fillers. Gravity fillers rely on the force of gravity to dispense products, while pressure fillers use air or pump systems to create a controlled flow.
Efficiency is a key advantage of pet filling machines. They can operate at high speeds, significantly increasing production capacity. Many models also feature easy adjustments for different container sizes.
Moreover, advanced technology ensures that these machines maintain product integrity by minimizing exposure to air during the filling process. This helps preserve flavor and freshness in sensitive liquids.
Investing in quality pet filling machinery contributes greatly to streamlined operations and enhanced product presentation on store shelves.
B. Can Filling Machines
Can filling machines are essential for industries dealing with beverages, food products, and even chemicals. They streamline the process of filling cans, ensuring consistency in volume and quality.
These machines come in various configurations to suit different production needs. Some are designed for carbonated drinks while others handle non-carbonated liquids. The versatility of can fillers makes them a staple in many manufacturing lines.
Efficiency is a key advantage. Automated systems can fill thousands of cans per hour, significantly reducing labor costs and time spent on production.
Moreover, modern can filling machines often incorporate advanced technology like sensors that detect fill levels and ensure accuracy. This minimizes waste and optimizes resource use.
However, maintenance is crucial for longevity. Regular checks help prevent downtime due to malfunctions or blockages during operation.
C. Jar Filling Machines
Jar filling machines are essential in many industries, especially food and cosmetics. They offer precise filling for products like sauces, jams, and creams. The design of these machines allows for quick adjustments to accommodate different jar sizes.
Most jar fillers operate on gravity or piston principles. Gravity fillers let the product flow into jars by gravitational force, while piston fillers use a mechanism to pump the liquid with accuracy. This versatility makes them popular choices across various sectors.
One standout feature is their ability to minimize waste. Efficient filling reduces leftover product in containers, leading to better yield and cost savings over time.
Moreover, modern jar filling machines often come equipped with automatic capping systems. This ensures that each container is sealed properly after being filled—crucial for maintaining freshness and preventing spillage during transport.
D. Other Types (Tube, Bottle, Pouch)
Filler machines come in various shapes and sizes, catering to unique packaging needs. Beyond the common pet, can, and jar filling machines, there are specific types designed for tubes, bottles, and pouches.
Tube filling machines handle products like creams or gels that require precise portioning. They ensure a clean fill with minimal waste.
Bottle fillers can accommodate diverse liquids ranging from beverages to industrial chemicals. Their adaptability makes them indispensable across multiple industries.
Pouch filling machines excel in packing snacks or powders efficiently. These machines often feature advanced technology for speed and accuracy while maintaining product integrity.
Each type of filler machine plays a critical role in streamlining production processes and meeting consumer demands effectively. Understanding these options allows businesses to select the best solutions for their specific needs.
Advantages and Disadvantages of Each Type
Pet filling machines are designed for high-speed production, making them ideal for companies that handle large volumes. They ensure precise fills and minimize product waste. However, they may require significant initial investment.
Can filling machines excel in maintaining the integrity of carbonated beverages. They provide a sealed environment to keep products fresh. Yet, these machines can be less flexible when dealing with different can sizes or shapes.
Jar filling machines offer versatility and can accommodate various jar dimensions easily. Their user-friendly design allows quick adjustments between batch runs. On the downside, they might not achieve the same speed as their counterparts.
Other types like tube fillers suit cosmetic and pharmaceutical industries perfectly but often need specialized setups for each product type. Pouch filling machines work well for liquids but may struggle with thicker substances while also requiring careful operator training to prevent spills or errors during processing.
Factors to Consider When Choosing a Filler Machine
Choosing the right filler machine is crucial for your production line. Start by assessing the type of product you’ll be filling. Liquids, powders, or granules each require different machinery.
Next, consider your production volume. High-output lines need robust machines that can handle constant use without downtime. For smaller operations, a semi-automatic option might suffice.
Think about the level of automation you desire. Fully automatic systems offer efficiency but come with higher costs and complexity. Manual and semi-automatic machines provide flexibility for various batch sizes.
Space availability in your facility plays a role too. Ensure that the dimensions of the machine fit within your operational area while allowing easy access for maintenance.
Evaluate budget constraints against features offered by different models to ensure you make an informed decision tailored to your specific needs.
Popular Brands in the Market
When it comes to filler machines, several brands stand out for their reliability and innovation. One of the most recognized names is Bosch Packaging Technology, known for its robust can filling systems that cater to various industries.
Another popular choice is Accutek Packaging Equipment Company. They offer a wide range of solutions, from semi-automatic to fully automatic machines. Their versatility makes them suitable for different production needs.
For those focused on precision, KHS GmbH excels with advanced technology in PET filling machinery. Their systems are designed to increase efficiency while maintaining product integrity.
Inline Filling Systems provides customizable options tailored to specific requirements. With a commitment to quality and customer satisfaction, they have built a strong reputation in the market.
These brands represent just a glimpse into the diverse options available today.
Maintenance and Safety Tips for Filler Machines
Regular maintenance is crucial for the longevity of filler machines. Keep a detailed schedule to check all components, including seals, nozzles, and pumps. This ensures optimal performance.
Always clean your machine after each use. Residue can build up and affect filling accuracy over time. Utilize food-grade cleaning solutions whenever necessary.
Safety should be a top priority when operating these machines. Ensure that all operators are trained properly on how to handle equipment safely. Wearing appropriate personal protective equipment (PPE) is essential.
Incorporate routine inspections into your workflow to identify any potential issues early on. Pay attention to unusual noises or changes in operation; these could signal a problem needing immediate attention.
Maintain an organized workspace around the filler machine. Clear away unnecessary items to prevent accidents and ensure easy access during maintenance tasks.
Conclusion
Understanding the different types of filler machines is essential for anyone involved in packaging operations. Each type serves a unique purpose and caters to various industries, from food and beverage to cosmetics and pharmaceuticals.
Pet filling machines are ideal for products stored in plastic containers, offering precision and speed. Can filling machines excel at packing beverages and other liquids into cans, ensuring minimal spillage. Jar filling machines provide versatility for a range of viscous products like sauces or creams, making them indispensable in many production lines.
Other options such as tube, bottle, or pouch fillers cater to niche market needs with specific design features that enhance efficiency. With each type comes its own set of advantages and challenges which should be weighed carefully against your business requirements.
When choosing the right filler machine, consider factors like product viscosity, container size, production speed, and budget constraints. Popular brands offer reliable machinery tailored to meet diverse operational demands while maintaining quality standards.
Maintenance plays a vital role in prolonging the lifespan of these machines; regular checks ensure they operate smoothly without interruptions. Safety protocols must also be followed diligently to protect operators during handling processes.
Investing time into understanding these various aspects can greatly influence your packaging success!